Nous allons vous expliquer les différents matériaux dont vous allez avoir besoin pour fabriquer une planche de surf:
1. Pain de mousse
Le pain de mousse, aussi appelé foam ou blanks en anglais, constitue le cœur de la planche.
La qualité du pain de mousse influence beaucoup la qualité du résultat final. Un bon pain de mousse résiste à la pression, est léger, blanc, ne vrille pas et est facile à travailler.
Il existe de nombreux fabricants de pain de mousse. Le type le plus utilisé pour la fabrication des planches de surf est le pain PU, à base de mousse polyuréthane.
Il est fabriqué en injectant de la mousse de polyuréthanne liquide dans un moule, la mousse gonfle et viens épouser la forme du moule.
Le pain de mousse est ensuite coupé en deux, et une latte de bois est insérée entre les deux parties du pain, pour donner plus de rigidité et de résistance à l´ensemble.
Les fabricants ont un catalogue de pain pour couvrir tous les besoins des shapers, de la planche de surf shortboard jusqu´au longboard.
L'autre type de pain de mousse est appelé EPS, il s’agit d’un pain de mousse de polystyrène, qui est utilisé pour la fabrication industrielle des planches epoxy, comme NSP ou Bic.
La mousse EPS peut seulement être utilisé avec de la résine époxy, elle n’est pas compatible avec les résines de polyester.
2. Résine de polyester
C´est la plus couramment utilisé. Plus facile et plus rapide à utiliser, elle est aussi plus économique que la résine époxy, c´est pour cela que 80% des planches de surf sont faites avec de la résine polyester.
La résine de polyester est mélangée avec un catalyseur qui déclenche le processus de catalisation, qui permet à la résine de durcir.
On peut utiliser un catalyseur liquide de type PMEC (méthyl éthyl cétone de peroxyde) qui réagit à la chaleur, ou un catalyseur Ultra-Violet qui active la catalisation sous l’action des rayons ultra-violet.
Il y a des milliers de résines de polyester sur le marché, mais attention à choisir une résine adapté et conçu pour la fabrication des planches de surf.
Chez monde-surf.com, nous avons sélectionné la Résine Silmar, la référence dans le monde entier, et la résine Hegardt H61-UV, une résine produite en Espagne et conçu pour l’industrie du surf.
3. Résine époxy
La résine époxy présente des propriétés mécaniques plus élevés que la résine polyester.
Elle est cependant beaucoup plus chère que la résine de polyester, et est donc moins utilisé.
Elle est surtout utilisée dans la fabrication industrielle de planches de surf, processus que maitrise particulièrement bien des marques comme NSP et Bic.
Méfiez-vous des planches "époxy" au même prix que les planches polyester. Ce sont souvent des planches chinoises, fabriqués avec de la résine époxy et une mousse de mauvaise qualité, le résultat étant bien inferieur a une planche polyester faites avec des matériaux de qualité.
Comme pour les résines de polyester, il existe des milliers de résines époxy, conçu pour des utilisations différentes.
4. Fibre de verre
La fibre de verre, une fois imprégnées de résine, donne résistance et rigidité à la planche de surf.
Les tissus de verre existent de différentes épaisseur, la manière dont les fibres sont tissés varie aussi, il y a de nombreux fabricants, avec une qualité qui varie aussi énormément.
Les fabricants de référence dans l´industrie du surf sont Hexcel, Aerialite et Shapers.
La norme consiste à utiliser une couche de fibre de verre 4Oz sur le bottom, et deux couches de 4Oz sur le pont.
Sur des planches fish, longboard ou rétro, on utilise souvent une couche de fibre de verre 4Oz et une couche de 6 oz sur le pont, pour renforcer la planche et lui donner plus d'inertie.
Le type de fibre le plus utilisé est la fibre de verre E-Glass.
Certaines planches haut de gamme sont fabriqués à partir de fibre de verre S-Glass, un tissu de qualité supérieure qui contient du Silice, et permet d'utiliser moins de fibres tout en obtenant la même résistance.
Cette fibre, deux fois plus cher que la fibre E-Glass, est souvent réservé aux rider pro et aux planches haut de gamme.
5. Styrène paraffiné
Le styrène paraffiné se mélange avec la résine de polyester dans une proportion de 5%, pour réaliser le hot-coat.
Il permet à la résine polyester de ne pas être collante, et de pouvoir être poncé.
6. Catalyseur PMEK
Le catalyseur PMEK se mélange avec la résine de polyester, afin d’activer le processus de catalisation, sous l'action de la chaleur.
Il est utilisé en fonction du poids de la résine, entre 1% et 3%, selon que la température est de 25 ou de 18 degrés. En dehors de ces températures, le catalyseur PMEK ne fonctionne pas bien.
Il est aussi possible de faire catalyser la résine UV avec un catalyseur PMEK, pour effectuer le travail de nuit par exemple, de sorte que la résine durcit même sans soleil.
7. Microbilles de verre
Les microbilles de verre sont mélangées à la résine pour obtenir un mélange de la consistance du yaourt.
Le rapport Poids/Volume est ainsi plus faible, ce qui est très utiles pour fixer les plug de leash, ou remplir un espace important sans générer trop de surpoids.
C’est un produit toxique à manipuler avec prudence, et toujours avec un masque.
8. Plug d´ailerons
Inventé dans les années 90 par FCS, cela a été une révolution.
Les plugs d´ailerons permettent de changer de dérives, et de les démonter lorsque vous voyagez en avion.
Les plugs FCS X2 originaux ont été copiés, et de nombreuses marques proposent maintenant des plug compatibles avec le système FCS, mais à un prix plus abordable, comme Eurofin.
Le système FUTURES FINS est une autre option, plus robuste, mais plus difficiles à monter. Vous trouverez également dans notre boutique en ligne les nouveaux systèmes FCSII et FCS Fusion.
Plug de leash M-Fins pour planche de surf Diamètre 30mm Blanc
Boîtier d'aileron de Longboard US Box M-Fins 10,5" Noir
Boîtier d'aileron de Longboard M-Fins US Box Fusion Blanc
9. Plug de leash
Le plug de leash est placé à environ 10cm du tail, pour pouvoir y attacher le leash.
Produits qui pourraient vous intéresser:
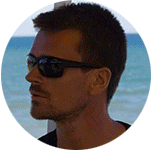
Sebas
Sebas est le créateur passionné et fondateur de Mundo-Surf, un espace dédié à ceux qui vivent et respirent le surf. Avec une connexion profonde avec l'océan et une passion débordante pour chaque vague, Sebas a transformé son amour pour le surf en une mission : partager, inspirer et éduquer la communauté.
En plus d'être un surfeur passionné, Sebas est un expert dans la fabrication de planches de surf, un art qui combine technique et créativité. À travers son blog, il propose non seulement des guides, des avis et des conseils, mais partage aussi son expérience dans la création de planches, aidant les autres à comprendre le processus derrière chaque design et matériau. Chez Mundo-Surf, Sebas nous invite tous à découvrir le surf dans son expression la plus pure, du bon équipement jusqu'à la fabrication personnalisée de planches.